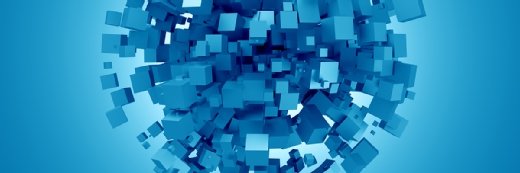
Getty Images/iStockphoto
Additive manufacturing: Learn about powder bed fusion
Powder bed fusion may cost less than other additive manufacturing approaches, but it can be time-consuming. Learn whether powder bed fusion is right for your manufacturing needs.
Powder bed fusion is one of several types of additive manufacturing. It can potentially benefit manufacturers because it may cost less than other additive manufacturing approaches and is a good approach for creating prototypes.
Powder bed fusion can be carried out using various materials, including powdered metals. However, the process can be time-consuming, and objects created through powder bed fusion usually need post-processing.
Here's more about powder bed fusion and how it relates to the supply chain.
What is powder bed fusion?
The powder bed fusion process involves a heat source warming powder to create a new object. The following steps comprise the full powder bed fusion process:
- A user creates a computer-aided design (CAD) template or model.
- Powder is deposited on the print bed.
- A heat source such as a laser moves across the powder layer, following guidance from the CAD template. The heat source fuses the powdered material, turning it into a solid.
- A second layer of powdered material is placed on top of the first layer.
- The heat source warms the new layer. These steps continue until the item is fully formed.
- Any extra powder or other material is taken off and the item is cleaned if necessary.
Powder bed fusion manufacturing in the supply chain
Powder bed fusion can be a valuable addition to manufacturing processes. The process's potentially lower cost compared to other additive manufacturing methods may make it a better fit for some manufacturers.
In addition to creating prototypes, powder bed fusion has been used to create objects ranging from fuel nozzles to prosthetics for medical patients.
Types of powder bed fusion manufacturing
Manufacturers can choose from the following powder bed fusion approaches:
- Selective laser sintering. During the selective laser sintering process, materials -- usually powdered polymers -- are heated and fused into a solid mass. During sintering, the powdered materials do not become completely melted.
- Selective heat sintering. This process involves a thermal printhead combining the powder into one object. This approach uses less heat and energy than other powder bed fusion processes.
- Direct metal laser sintering. Direct metal laser sintering is like selective laser sintering but incorporates metals instead of polymers. While sintering is part of the name, the metals are melted.
- Selective laser melting. While selective laser melting is similar to selective laser sintering, the powdered material is completely melted during selective laser melting and the process takes less time.
- Electron beam melting. During the electron beam melting process, an electron beam blends material together instead of a laser beam. The electron beam melting process results in a stronger finished object than other powder bed fusion approaches because the heat is spread evenly over the object.
The type of material used during powder bed fusion depends on the specific powder bed fusion process. For example, selective laser melting incorporates metals such as aluminum and titanium, while selective heat sintering uses nylon.
Meanwhile, electron beam melting uses materials such as titanium and copper.
The pros and cons of powder bed fusion
Powder bed fusion can provide several advantages for manufacturers. The powdered materials from the powder bed fusion process are recyclable, which minimizes waste, and the process is versatile because it can be carried out using multiple materials.
Powder bed fusion is also capable of producing parts with better resolution than some other additive manufacturing approaches.
However, powder bed fusion does also have some disadvantages. It can be a time-consuming process, so it's not ideal for high-production runs. In addition, manufacturers must take item size into account, as powder bed fusion can only create items that can fit on the print bed.
Also, the required post-processing can require more time and expense.